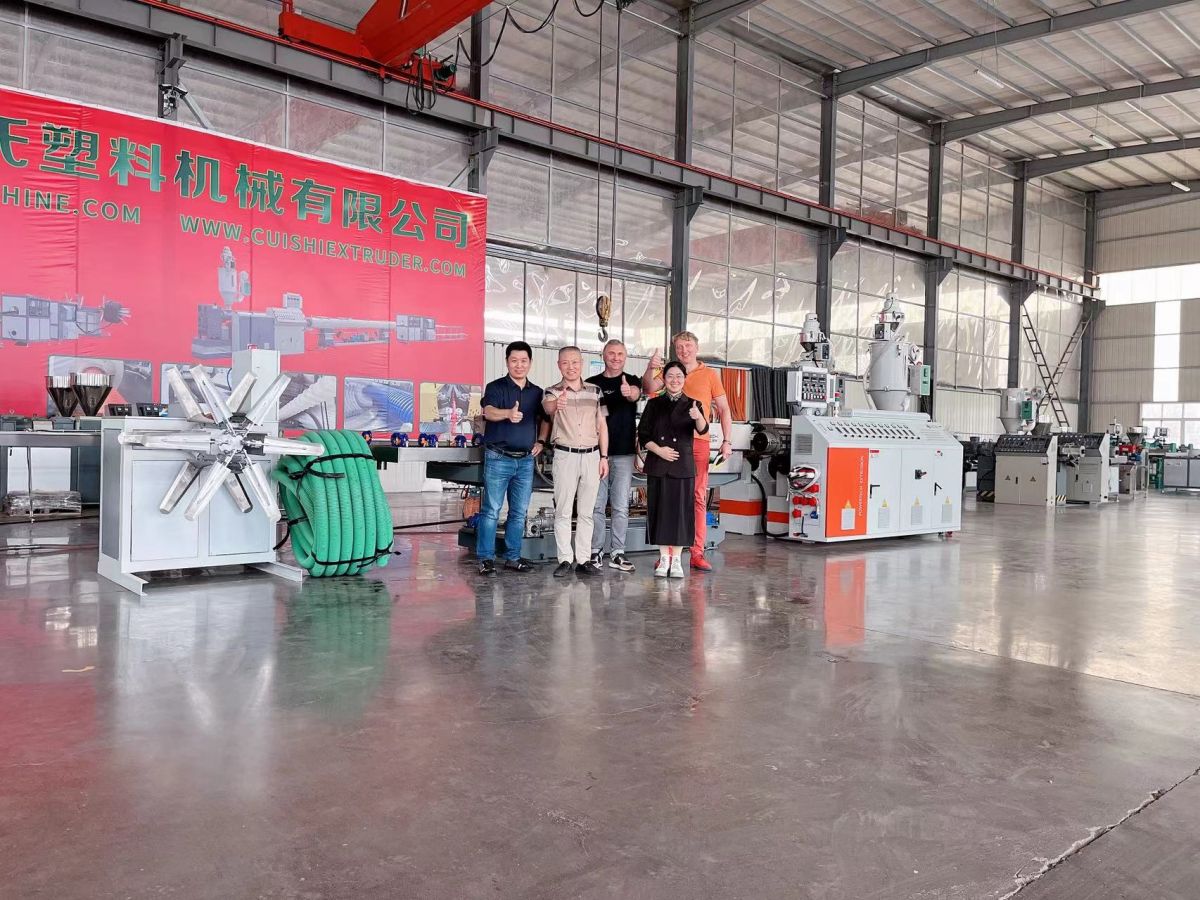
Unsere doppelwandige Wellrohrmaschine ist vielseitig einsetzbar.Es können einwandige Wellrohre, doppelwandige Wellrohre, doppelwandige perforierte Wellrohre, Tunnel-Blindrohre gegen Kristallisationswasser, Frischluftkanäle für die Innendekoration und Bambusrohre hergestellt werden.Wir können die Form ändern.Alles gut
Frischluftkanal, PE-Spezialwellrohr für Luftwechsel, Windkasten, Lüftungsschlauch, Stützlüftungsrohr
Frischluftsystem Wellrohr 75/110PE Rohr Doppelwandiges Kunststoffrohr Frischluftkanal Klimaanlage Lüftungsschlauch
Frischluftsystem Doppelschichtwellrohr Frischluftkanal PE-Rohr 75, 110, 160
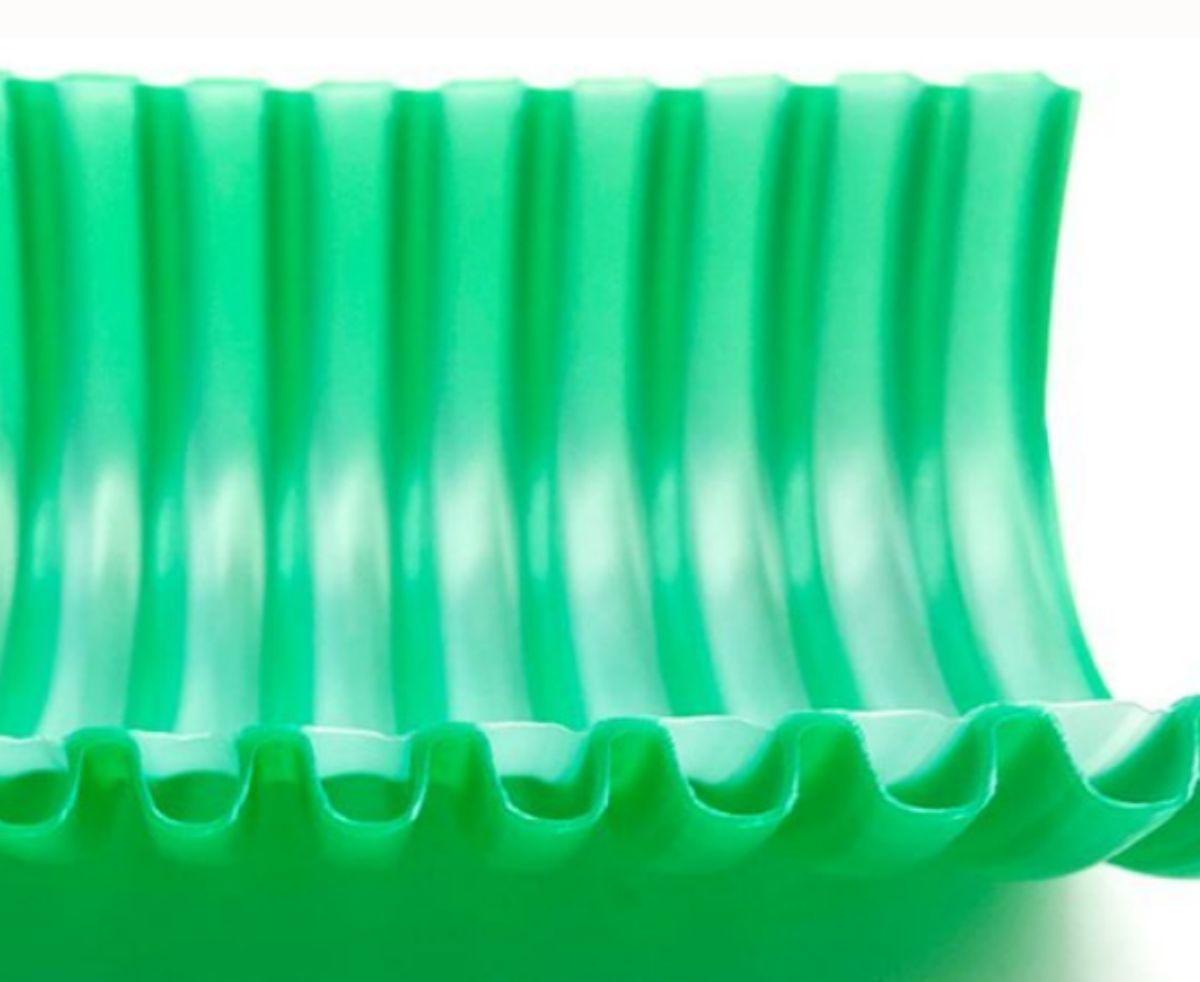
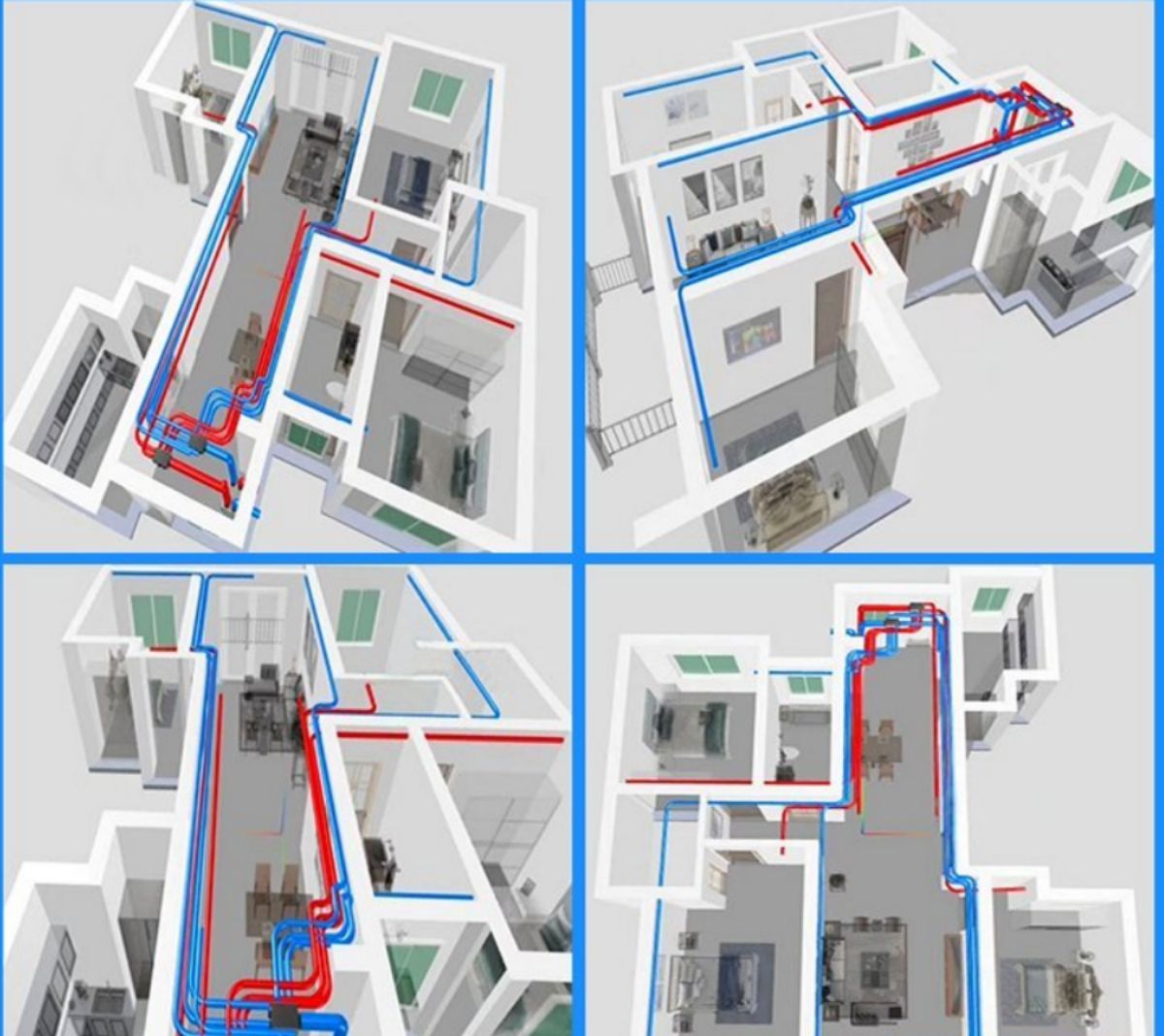
PE-Rohr 75 Luftkanal-Abluftschlauch PE-Rohr Frischluftsystem Doppelwandiger Wellschlauch
Das Frischluftsystem basiert auf der Verwendung spezieller Geräte auf einer Seite eines geschlossenen Raums, um Frischluft in den Raum zu leiten und sie dann über spezielle Geräte auf der anderen Seite nach außen abzuführen.Im Innenbereich wird ein „Frischluft-/Strömungsfeld“ gebildet, um den Bedarf an Frischluft in Innenräumen zu decken.Der Umsetzungsplan besteht darin, Ventilatoren mit hohem Winddruck und großem Durchfluss zu verwenden, sich auf Maschinen zu verlassen, um Luft von einer Seite dem Raum zuzuführen, und einen speziell entwickelten Abluftventilator zu verwenden, um sie von der anderen Seite nach außen abzuführen, um die Bildung von a zu erzwingen Frischluft-/Strömungsfeld im System.Bei der Luftzufuhr wird die in den Raum eintretende Luft gefiltert, mit Sauerstoff angereichert und (im Winter) vorgewärmt.
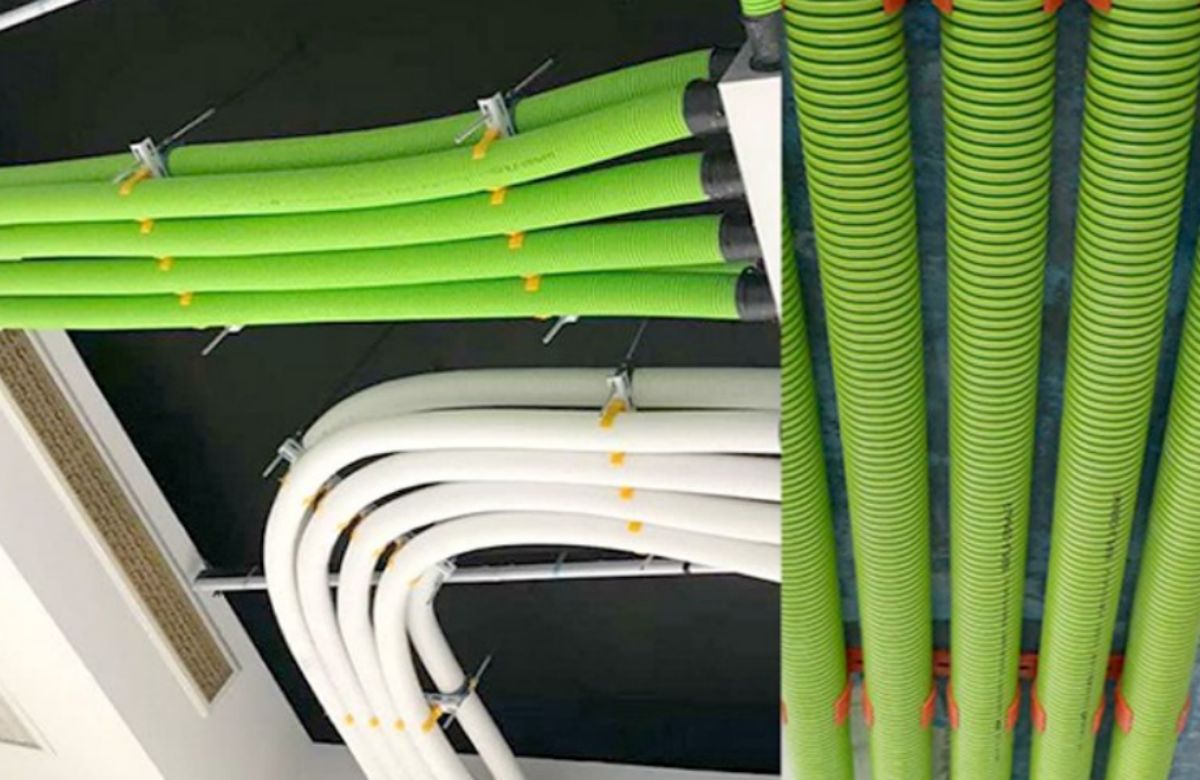
Die neue Luftkanalausrüstung besteht aus: Außenwandträger + Innenwandträger + Maschinenkopf + Form + Formmaschine + Wickelmaschine
Es wird empfohlen, dass Kunden eine allgemeine Erdung durchführen und ein 6 Meter langes Kupferkabel verlegen, um alle Maschinen zu verbinden und gleichzeitig zu erden.Die Formmaschine und die Wickelmaschine sind alle mit 380 V ausgestattet.Die installierte Gesamtleistung beträgt 65 Kilowatt, die tatsächliche Produktion beträgt 25 Kilowatt (25 Kilowattstunden).
Es wird empfohlen, dass der Abstand zwischen der Formmaschine und der Wickelmaschine 6 Meter beträgt
Der Abstand vom Außenwandträger zur Formmaschine beträgt 825 mm und der Abstand vom Innenwandträger zur Formmaschine beträgt 785 mm.
Als wir ein einwandiges Wellrohr entwickelten, schalteten wir einfach einen Innenwand-Extruder ab.
Sie können auch einen Drahtvorschub für Stahldraht hinzufügen, um ein Wellrohr für die Stromverkabelung herzustellen.Das Loch für den Eisendraht sollte in die Form gebohrt werden.Der Durchmesser des Eisendrahtes sollte 1,0 mm nicht überschreiten.Der verwendete Wassermantel sollte ebenfalls durch einen hohlen zweischichtigen Mantel ersetzt werden.
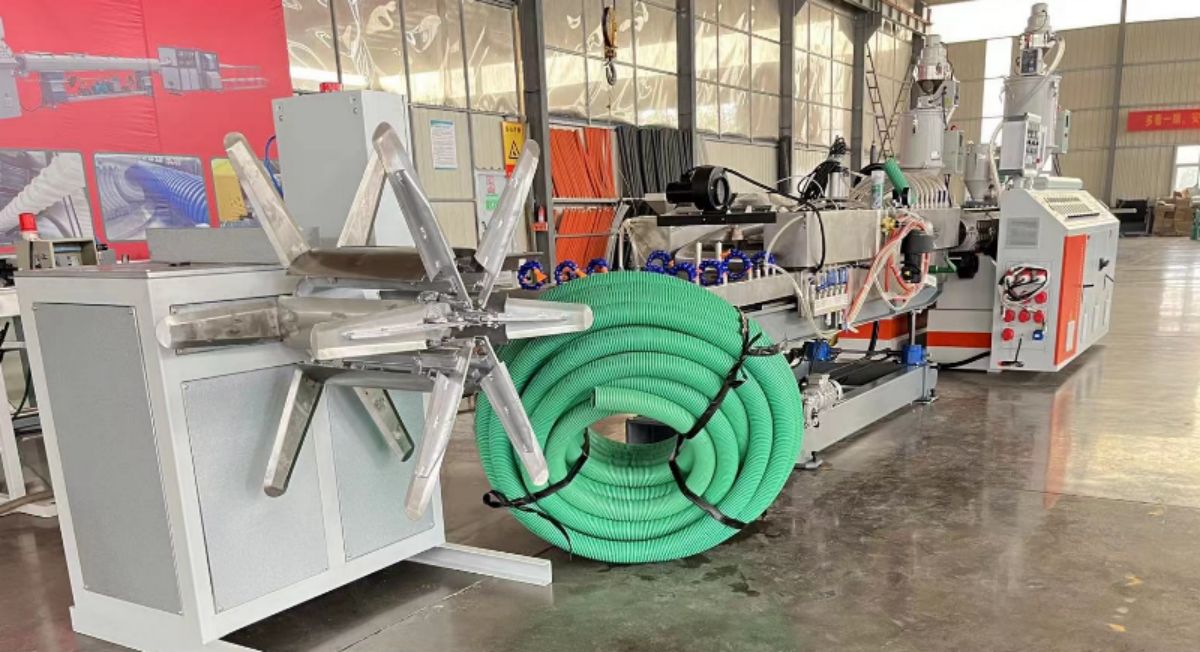
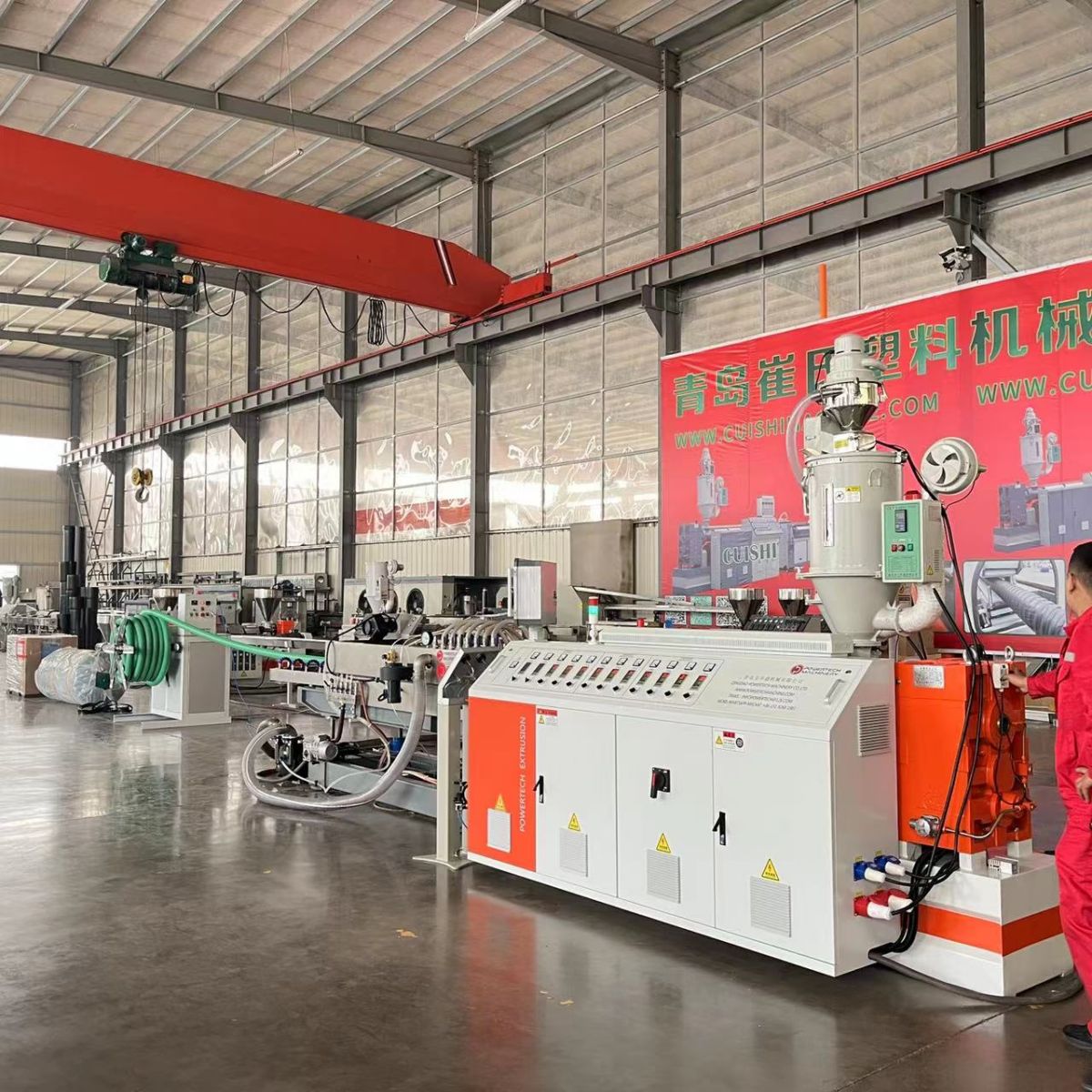
Der Extruder wird je nach Materialqualität 1,5 bis 2 Stunden lang auf 200 bis 220 Grad erhitzt.Die Bereiche vier und fünf des Maschinenkopfes sind die Backup-Bereiche.Nachdem die Temperatur die Temperatur erreicht hat und nachdem die Wirtsform und die Formmaschine ein Gleichgewicht gefunden haben, ist die Rahmenebene der Werkzeugmaschine. Um sicherzustellen, dass sie genau ist, legen Sie die Wasserwaage auf die Form, um sie zu nivellieren.Achten Sie nach dem Nivellieren darauf, die 12 Schrauben auf der linken und rechten Seite der Form festzuziehen.Wenn es nicht nivelliert ist, kommt das Material nicht heraus und der Maschinenkopf reibt an der Form.An der Formmaschine gibt es Einstellschrauben nach oben, unten, links und rechts.
Beim Nivellieren müssen Sie darauf achten, dass Sie nach dem Vorwärmen möglichst genau ein wenig Material herausdrücken und dann das Gleichgewicht finden.
Passen Sie die Durchbiegung der Außenwand an und verwenden Sie dann einen Kreis großer Schrauben am Heizband am Maschinenkopf.Welche Seite der Außenwand ist dicker, welche Seite ist fester und welche Seite ist lockerer;Passen Sie die Durchbiegung der Innenwand an, und dann gibt es 4 kleine Schrauben an der Matrize. Welche Seite ist dünner?Die Innenwand und die Außenwand liegen sich gegenüber.
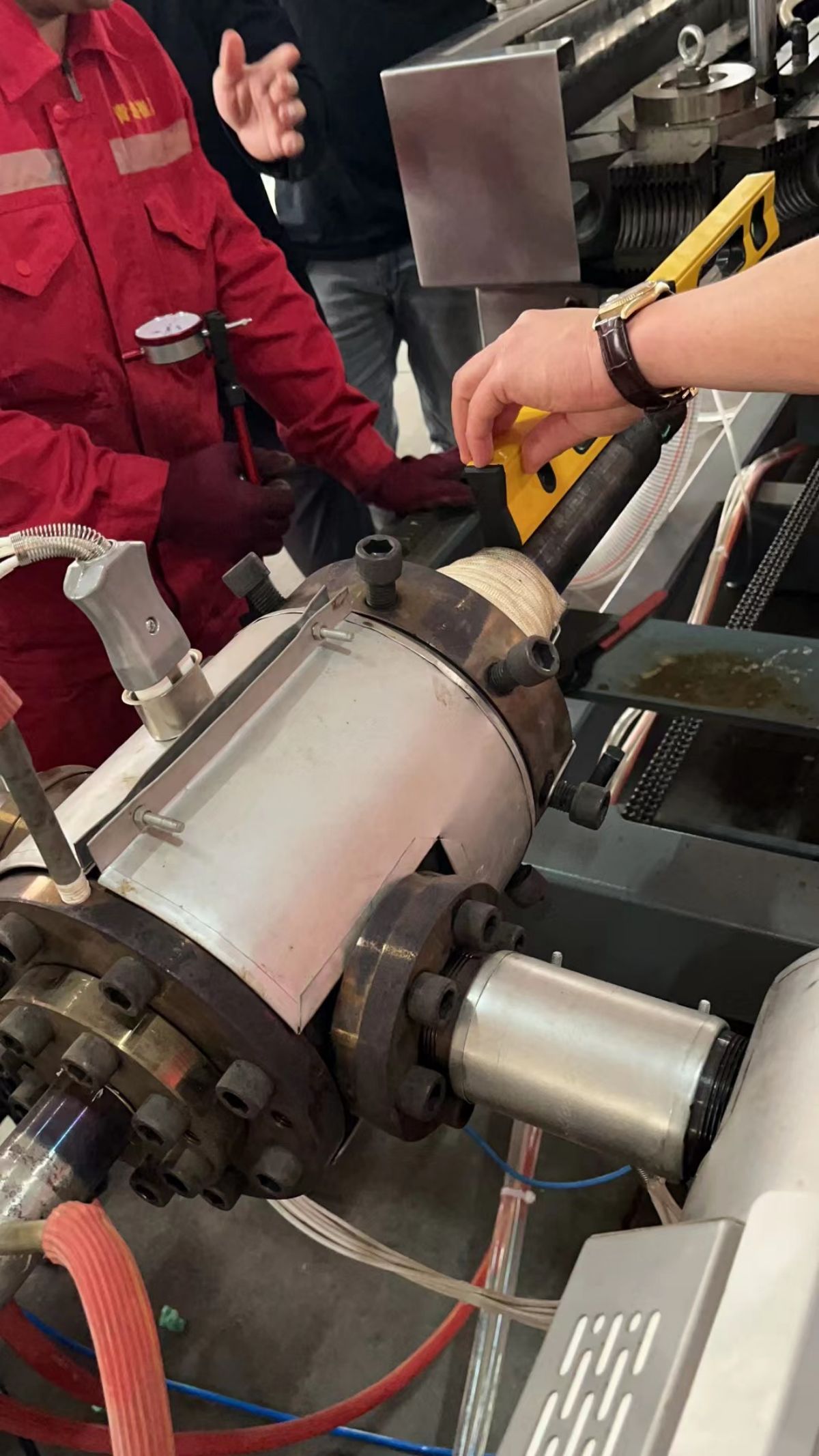
Starten Sie die drei grünen Tasten (Außenwand, Innenwand und Formmaschine am Kragarmkasten).Die Geschwindigkeit der Außenwandmaschine beginnt bei 272 – der normale Betrieb beträgt 290 U/min, die Geschwindigkeit der Innenwandmaschine beträgt 265 – der normale Betrieb beträgt 214 U/min, die Geschwindigkeit der Formmaschine beträgt 614 U/min und die Geschwindigkeit der Formmaschine wird während der nachfolgenden Produktion beschleunigt.Bei 704 U/min beträgt der Hoststrom 16 A, wodurch die Wandstärke dünner wird.Bei der Herstellung eines neuen Luftkanals sollte die Innenwand nicht zu dick sein, da sonst die Innenwand keine gute Krümmung aufweist.
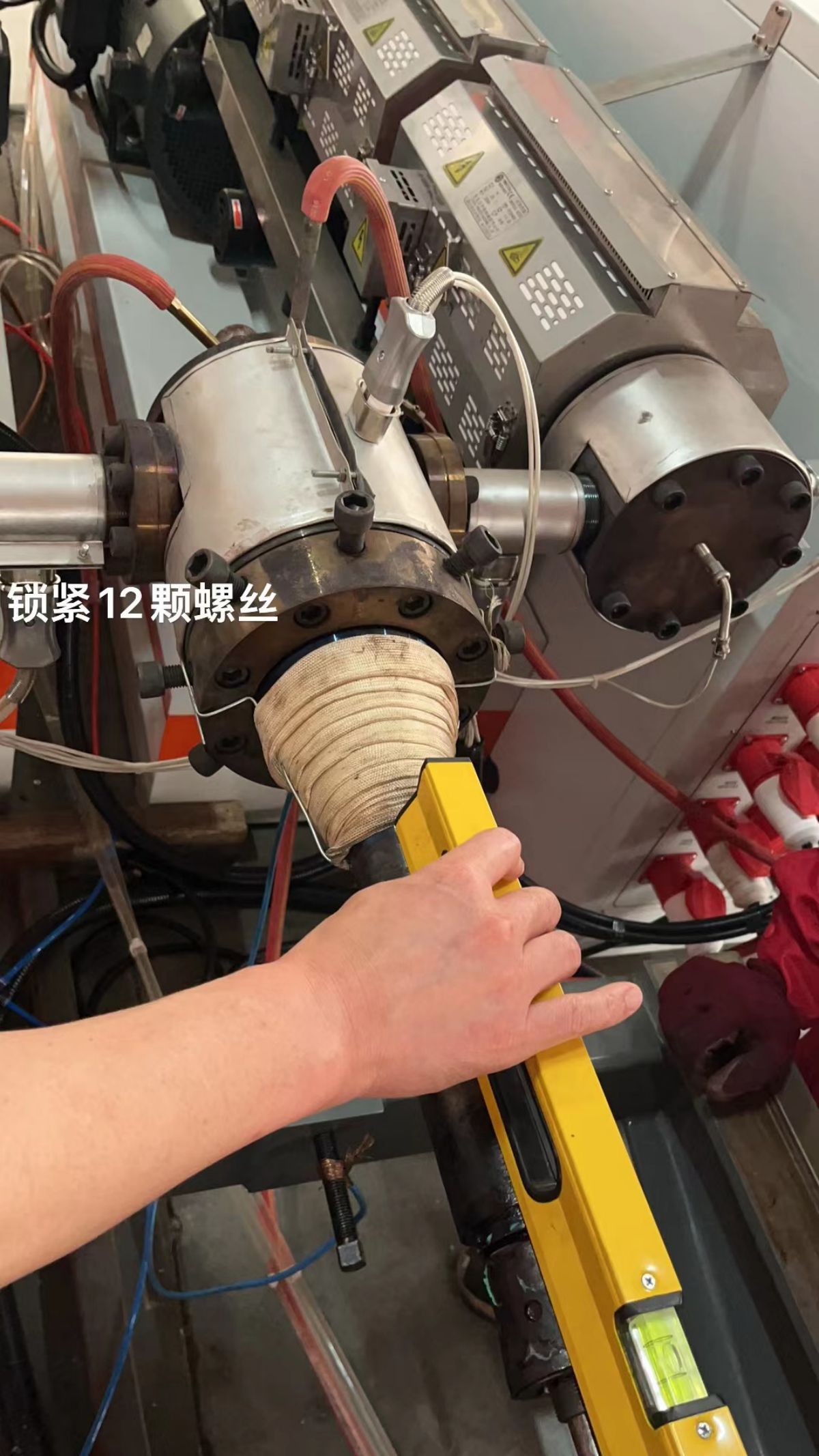
Beim gleichzeitigen Einschalten des Luftdrucks an den Innen- und Außenwänden wird empfohlen, dass der Innendruck zwischen 0,02 und 0,04 liegt und der Außendruck ähnlich ist.Finden Sie einen Gleichgewichtspunkt.Der Luftpumpenschlauch muss dicker sein, um einen stabilen Luftdruck zu gewährleisten.Die internen und externen Luftdruckmesser müssen stabil sein und dürfen nicht schwanken., sonst wird es den Wellenkamm beeinflussen.Wenn die Außenwand dünn ist, muss das Vakuumsystem nicht verwendet werden.
Der 15-kW-Luftkompressor kann 4 Leitungen versorgen.Es wird empfohlen, ein Luftrohr mit 40 mm Durchmesser und 0,5–0,6 MPA zu verwenden.Der Innenwanddruck ist größer als der Außenwanddruck, und die Innenluft ist größer als die Außenluft, da an der Innenwand ein R-Winkel vorhanden ist.Überprüfen Sie bei der Inbetriebnahme den Betriebsstrom.Der Wechselrichter wird eingeschaltet und der Strom wird angezeigt, 50 % 7042 und 50 % 5502, die Innenwand beträgt 5 kg, die Außenwand beträgt 12 kg und die Außenwand beträgt das 2- bis 3-fache der Innenwand.
Von links nach rechts befinden sich auf dem Formkernstab an der Formmündung die Außenluft, die Außenwand, die Innenluft und die Innenwand.
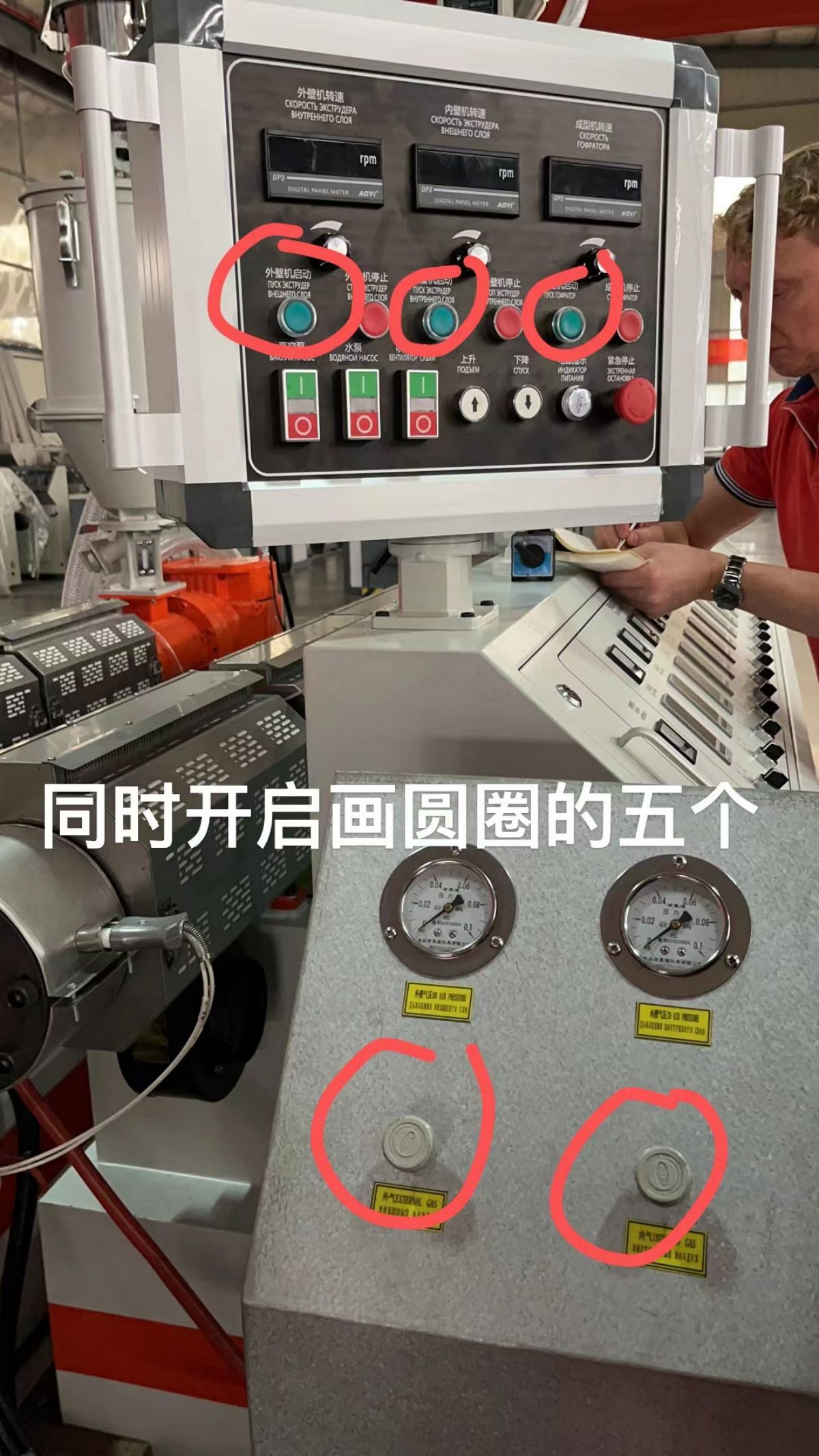
Öffnen Sie verschiedene Wasserkanäle der Formmaschine
Der Vakuummeter an der Formmaschine beträgt etwa 0,08.Unmittelbar rechts davon befindet sich das Überdruckventil des Vakuummeters.
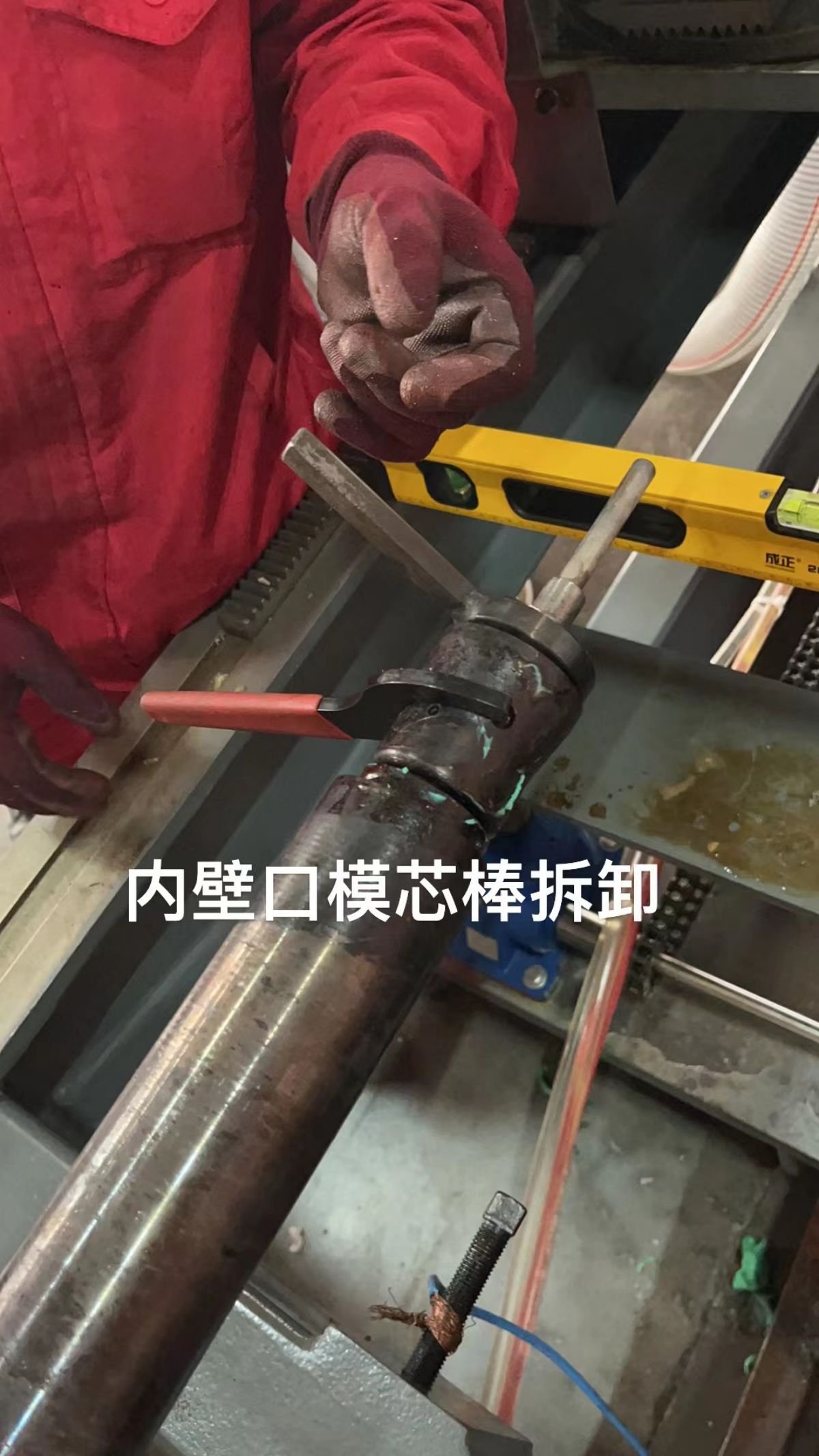
Wenn der grüne Dichtungsring des Wassermantels gebrochen ist, kommt es zu Undichtigkeiten.Überprüfen und ersetzen Sie es regelmäßig.
Öffnen Sie nach dem Drehen des Wassermantels rechtzeitig das Wassermantelventil auf der äußersten rechten Seite der Formmaschine bei geöffneter Auf- und Abwärtsrichtung, um zu verhindern, dass der O-Ring des Wassermantels durch die Hitze des Maschinenkopfs verbrannt wird .
Ziehen Sie den Wassermantel beim Einbau fest und drehen Sie ihn etwas zurück.Der Zweck besteht darin, eine natürliche Ausrichtung des Wassermantels nach oben, unten, links und rechts zu ermöglichen.Wenn sich die Formmaschine dem Wassermantel nähert, halten Sie den Wassermantel hoch.
Die Matrize an der Außenwand sollte mit einem Abstand von 345 mm auf die Position des Presszylinders ausgerichtet sein (wie im Bild gezeigt).
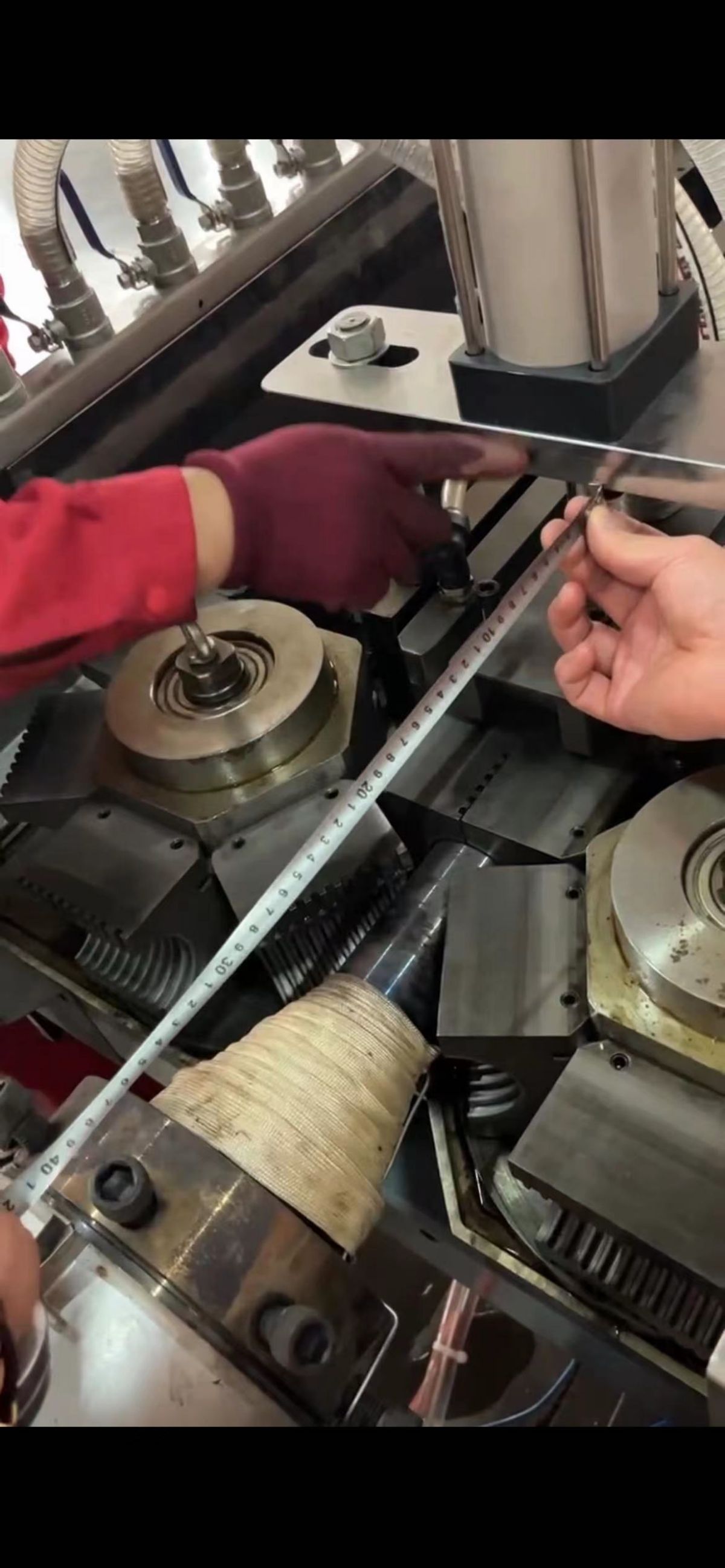
Wenn Sie einen Wassertank bauen, müssen Sie über einen Filter verfügen und reines Wasser verwenden.Wasser mit Ablagerungen blockiert den Wassermantel und die Wasserpumpe.
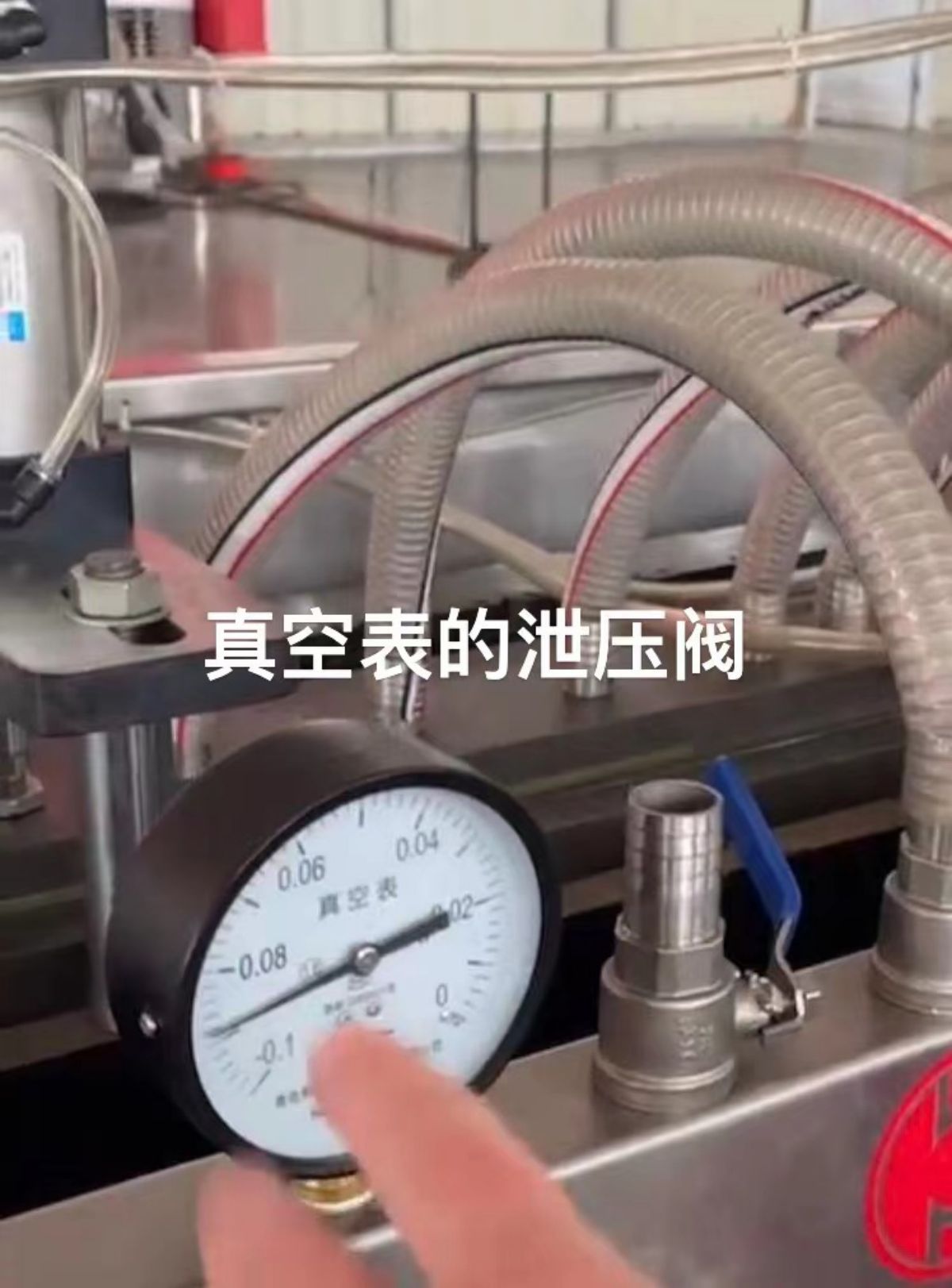
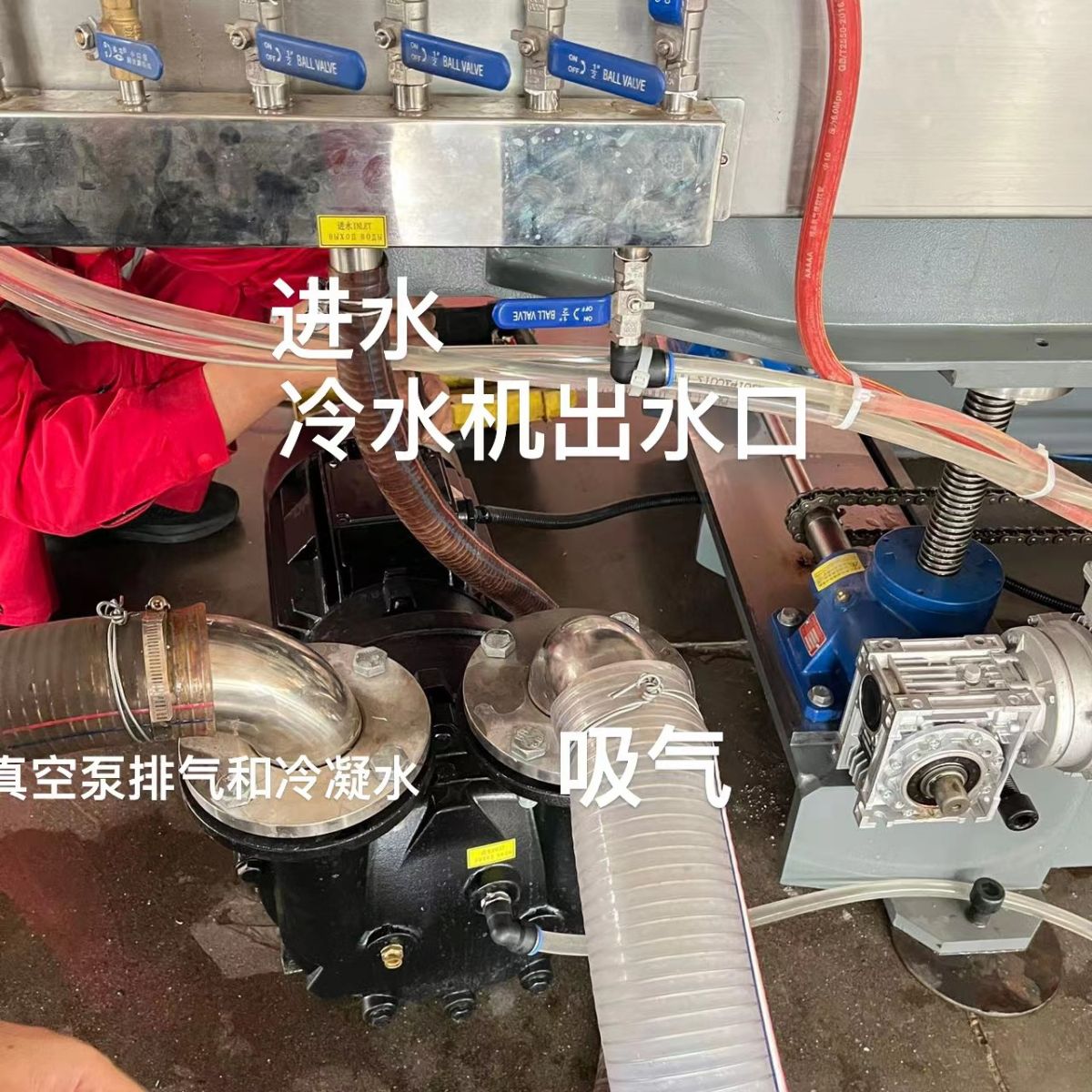
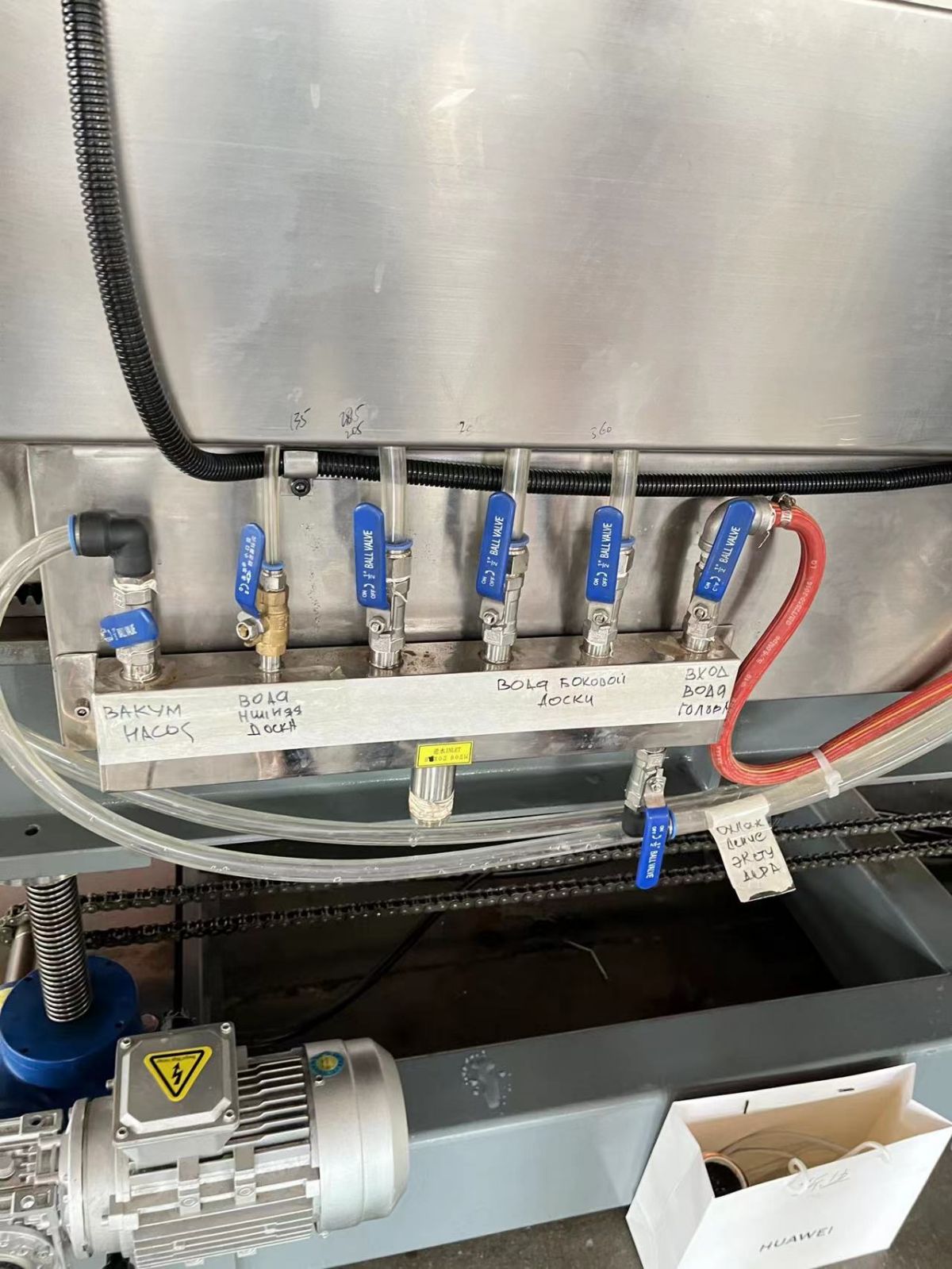
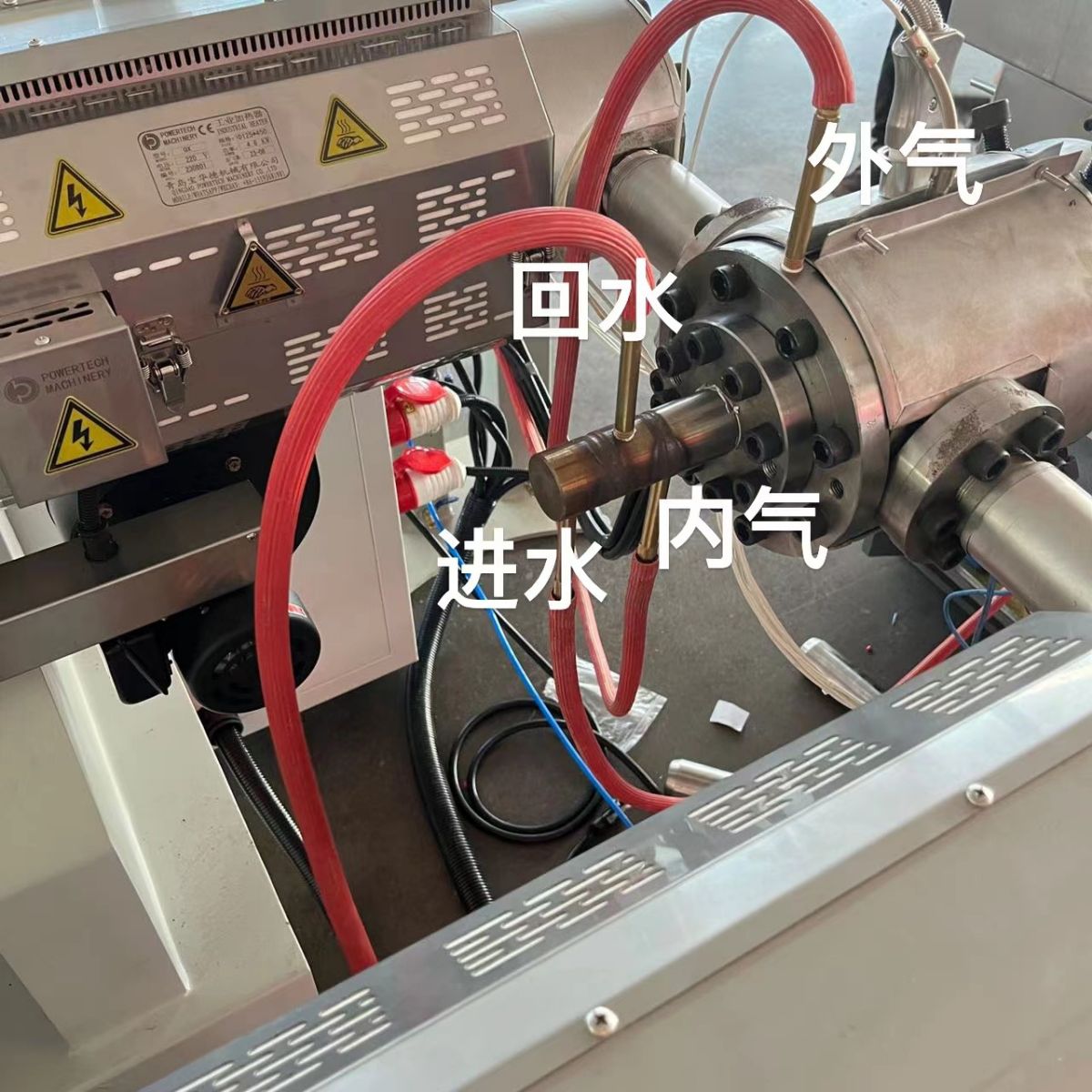
Schritte zum Herunterfahren:
Stoppen Sie zuerst die Hauptmaschine, die Hauptmaschinen für die Außenwand und die Innenwand, warten Sie, bis das Material austritt, stoppen Sie dann die Formmaschine und entfernen Sie sofort den Wassermantel.Der Wassermantel ist kalt und kann direkt von Hand gedreht und dann der Hauptknopf des Schaltschranks geschlossen werden (horizontal horizontal).Der Strom ist in der linken und rechten Richtung ausgeschaltet und der Strom ist in der Auf- und Ab-Richtung eingeschaltet.Bevor Sie die Maschine das nächste Mal starten, achten Sie darauf, zuerst den Matrizendorn des Maschinenkopfes erneut zu erwärmen, da sonst das Material im Inneren erstarrt.Wenn es nicht erhitzt wird, kann es leicht platzen.
Die Vakuumpumpe kann für den Kühler verwendet werden, die Wasserpumpe wird jedoch nicht benötigt.Es ist einfach reserviert.
Es wird empfohlen, dass Kunden eine allgemeine Erdung durchführen und ein 6 Meter langes Kupferkabel verlegen, um alle Maschinen zu verbinden und gleichzeitig zu erden.Die Formmaschine und die Wickelmaschine sind alle mit 380 V ausgestattet.Die installierte Gesamtleistung beträgt 65 Kilowatt, die tatsächliche Produktion beträgt 25 Kilowatt (25 Kilowattstunden).
Beim Formwechsel Hebeknopf, 70-kg-Druckplatte
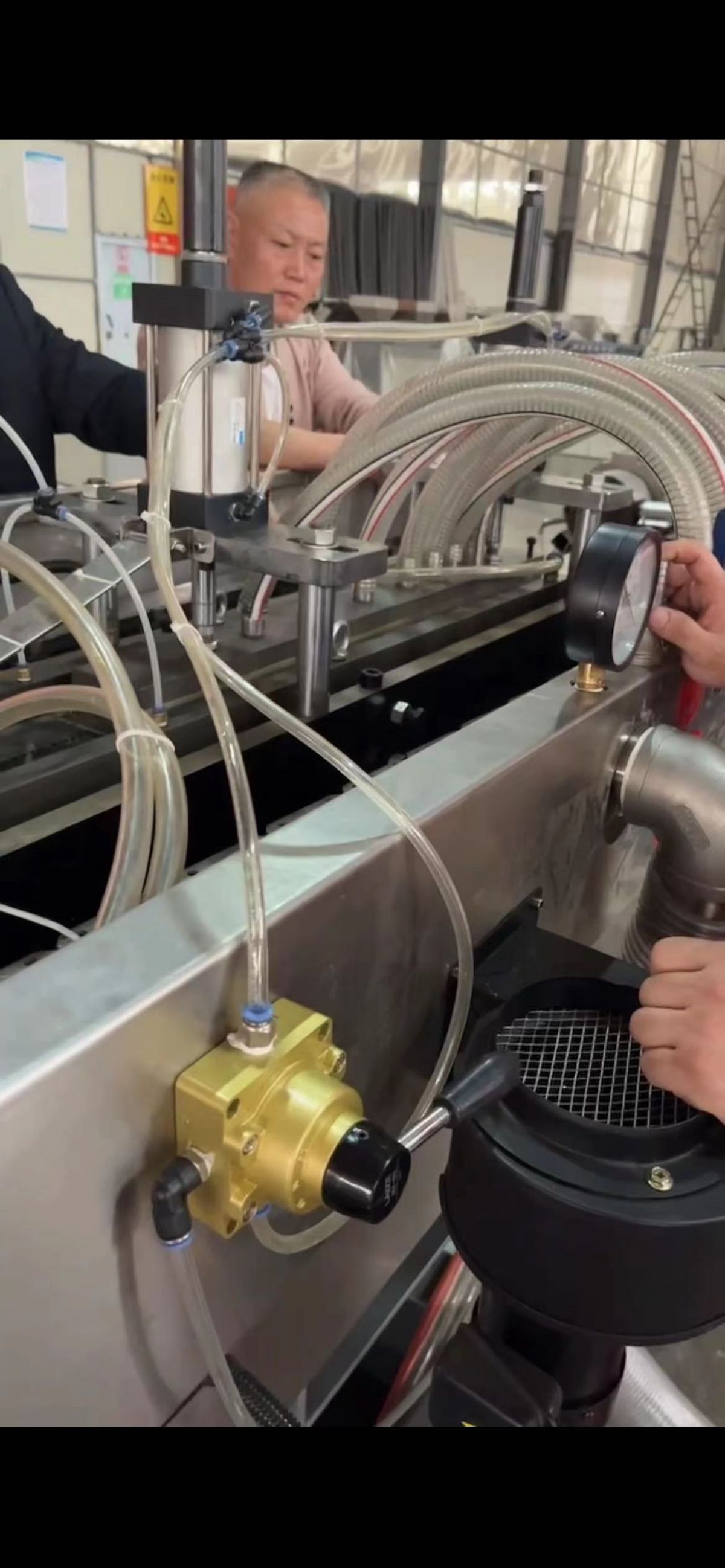
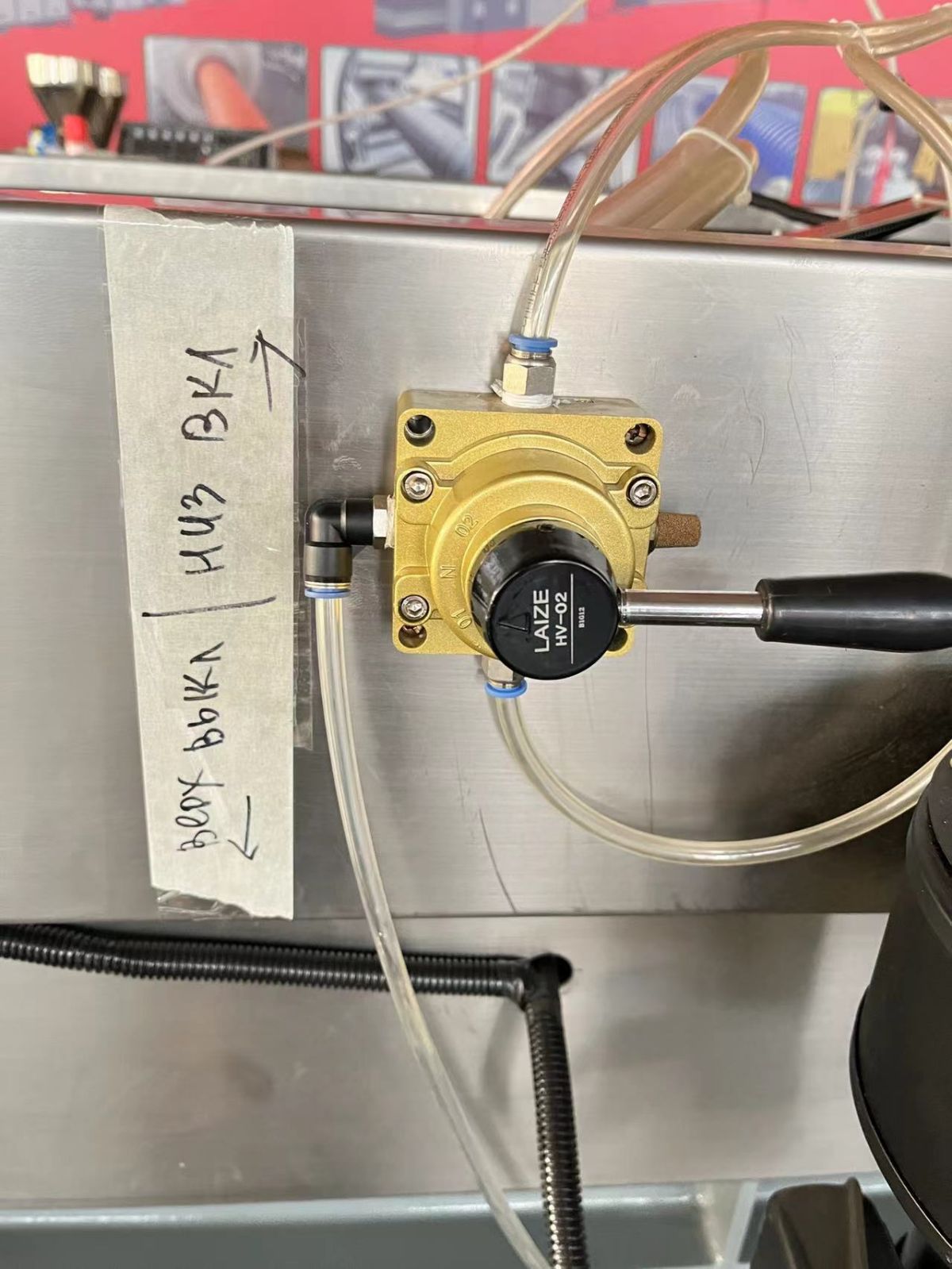
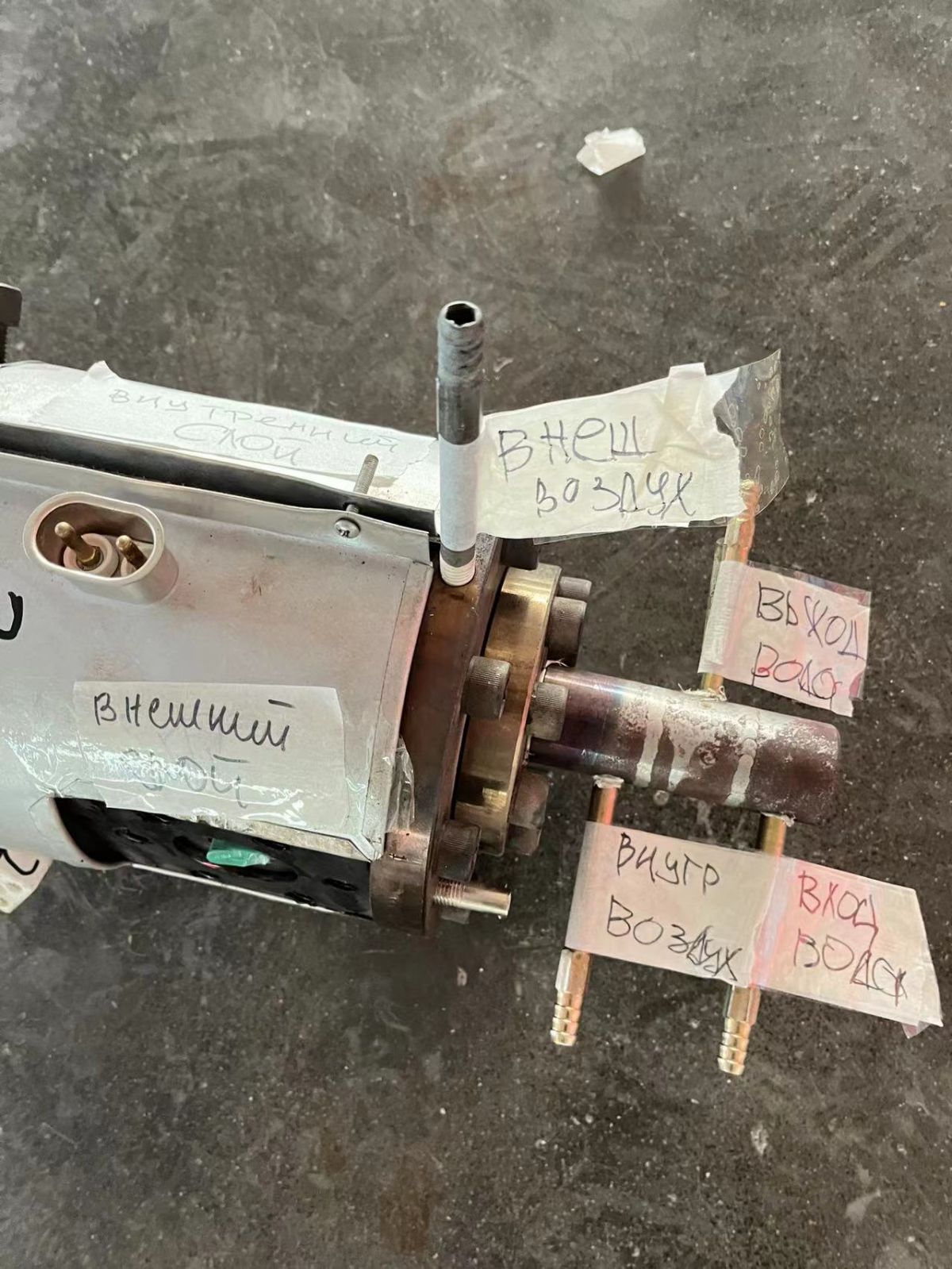
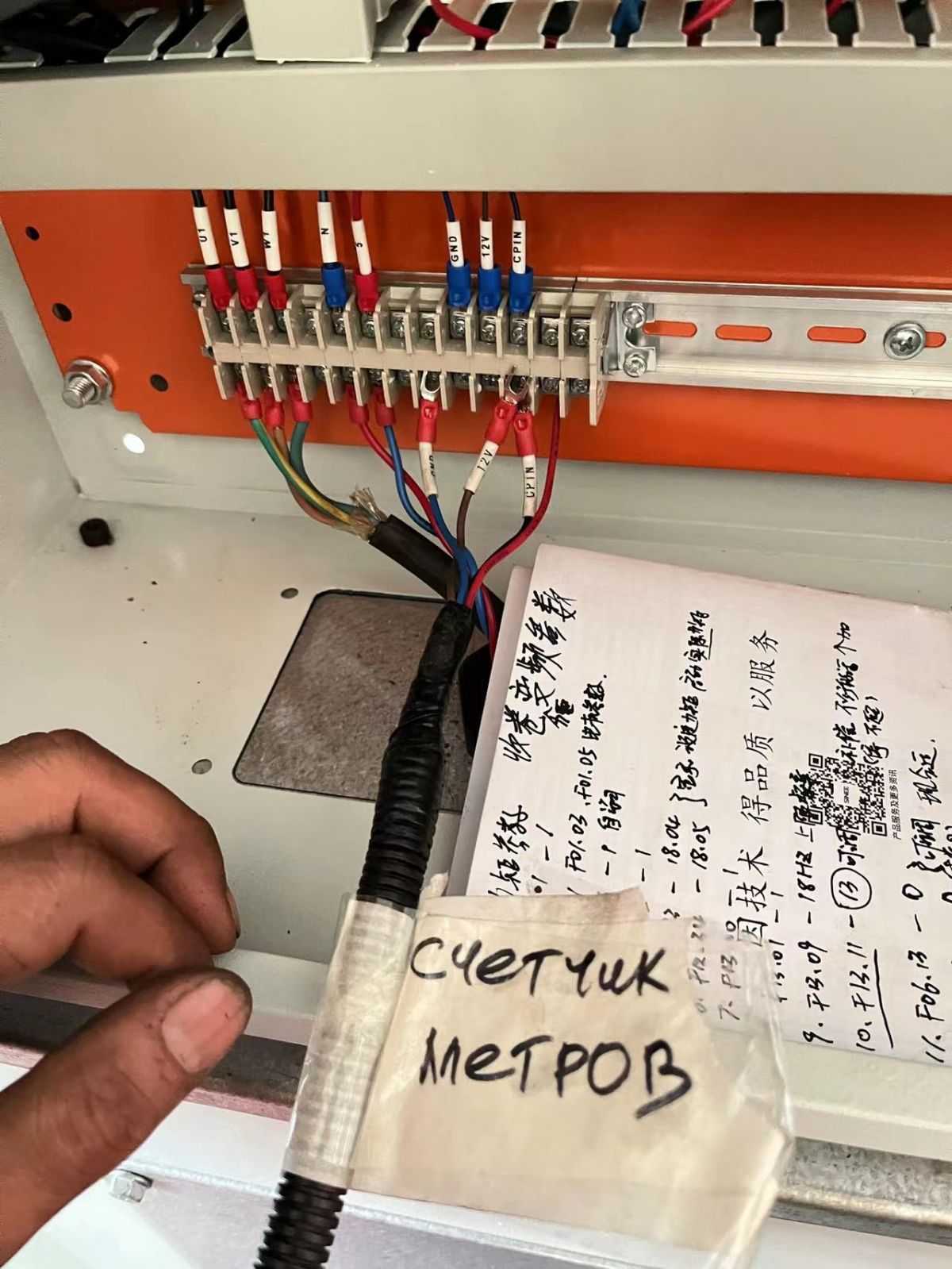

Zeitpunkt der Veröffentlichung: 16. Okt. 2023